Introduction to Warehouse Standard Operating Procedures
Whether you are managing an expansive, multinational distribution center or running a modest local warehouse, the heart and soul of your operations invariably come down to one vital aspect: ‘Warehouse Standard Operating Procedures’ (SOPs). Without these well-defined procedures, even the most efficient warehouse can quickly become chaotic.
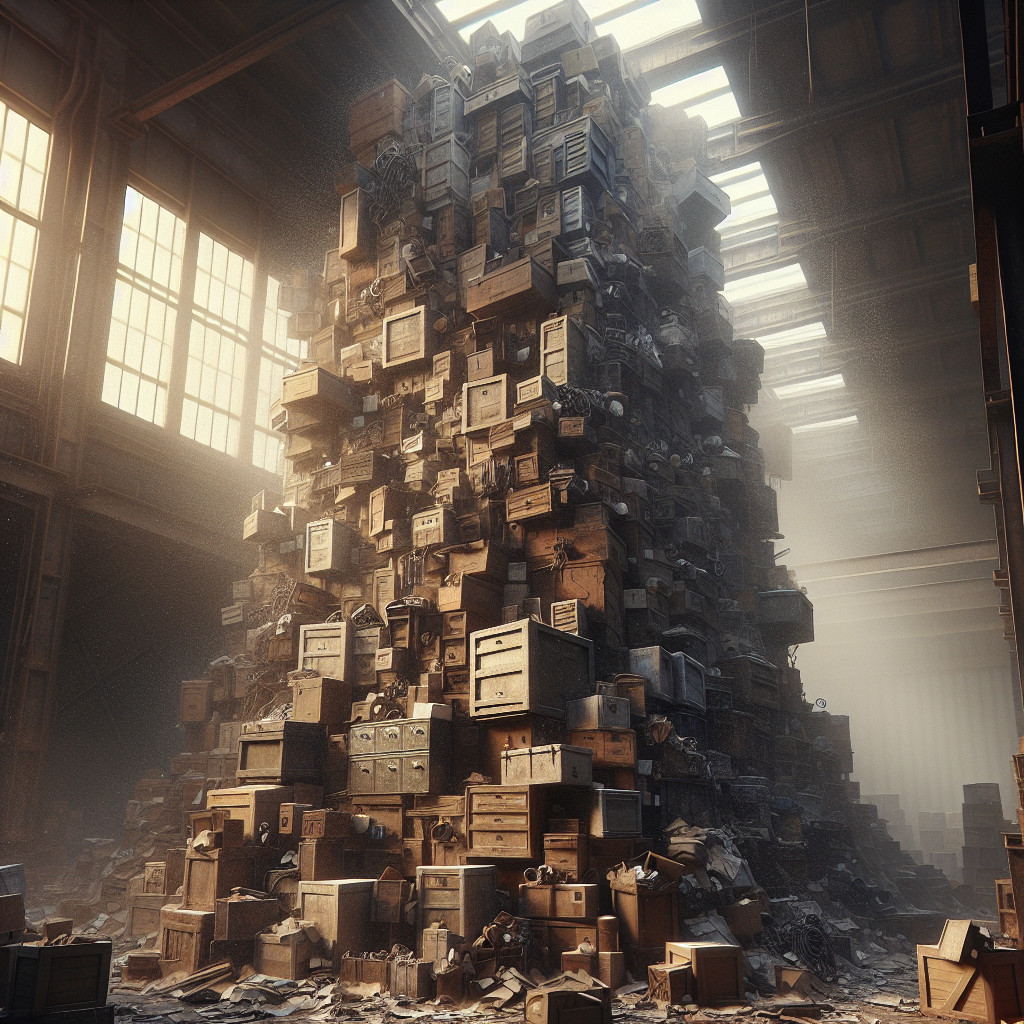
Guess What! We have an AI Powered SOP Generator that you can use to generate a custom SOP tailored to your warehouse.
SOPs act as the circulatory system for warehouses. They dictate how every task should be carried out—from receiving inventory and keeping track of products to order fulfillment and ensuring safety practices. The main objective of ‘Warehouse SOP’ is to create a systematic, organized environment that can efficiently manage the thousands of moving parts involved in warehouse operations.
Standard operating procedure for a warehouse entrusts your team with a clear roadmap on handling daily operations, reducing the scope for errors, maintaining consistency, and boosting productivity. It’s akin to putting together a giant puzzle: without each piece being in its right place—fitted in by following designated guidelines—it’s hard to visualize the complete picture.
Imagine a scenario where there are no structured SOPs in place. Everything seems unpredictable! Workers would be unsure of their tasks, safety protocols might be sidelined, and most alarming—a potential increase in errors and discrepancies in inventory management. Such disorder not only leads to massive inefficiency but also escalates operational costs.
The Role of Warehouse SOP
The role of ‘Warehouse Standard Operating Procedures’ goes beyond just keeping things in order. They define roles, set expectations and standards which aid your employees in understanding their responsibilities better. A robust SOP in place accentuates accountability and promotes a culture of transparency and efficiency.
The lack of well-defined SOPs often leads to operational inconsistencies like improper stockpile organization or aisle congestion. These issues subsequently affect the ease of product retrieval and overall warehouse functionality.
For example, an optimal ‘Warehouse and Inventory Management SOP’ can streamline the goods receiving process, create efficient space utilization strategies, manage stock levels effectively, and ensure swift and accurate order fulfillment—making your warehouse engine run smooth and efficient.
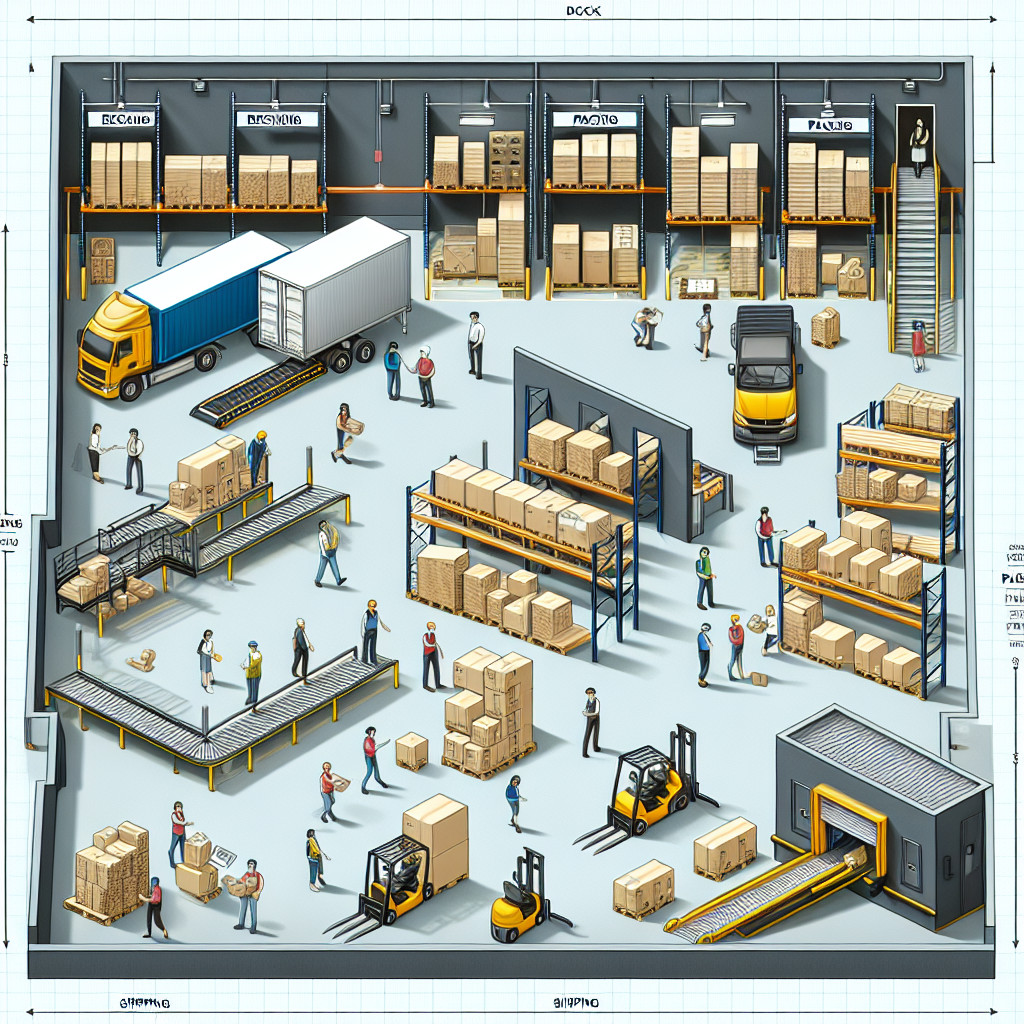
The Imperative of Warehouse Standard Operating Procedures
In essence, standardized operating procedures stand as a shield against chaos, confusion, and the randomness that could potentially plague a warehouse environment. Layered with clarity, consistency, accountability—SOPs equip you with the necessary tools to effectively juggle various aspects of warehouse operations. They enable a seamless flow of processes and people, creating a harmonious symphony of efficiency and productivity.
Absence of such procedures is akin to sailing in a rudderless ship amidst choppy seas; it’s not a question of ‘if’, but ‘when’ you will hit an iceberg! It’s time to take control and steer your warehouse operations towards a potential goldmine of efficiency and productivity using well-crafted ‘Warehouse SOPs’.
Detailed SOPs for Different Areas in a Warehouse
While it’s integral to understand the importance of warehouse SOPs, it is equally crucial to learn how these SOPs work within different sections of a warehouse. Each department or area requires a carefully designed and thought-out procedure to ensure optimal efficiency and productivity.
Warehouse and Inventory Management SOP
Without an effective ‘Warehouse and Inventory Management SOP’, managing the multitude of items coming in and going out of your warehouse can easily turn into an uncontrollable chaos. An optimal inventory management SOP includes strategies for space utilization, stock level management, order tracking, and more. It guides personnel on the process of receiving shipments, verifying them against purchase orders, appropriately storing them within the warehouse, and finally moving them out when needed.
This detailed roadmap not only prevents overstocking or understocking issues but also aids in achieving quicker order processing times while reducing errors in order picking and shipping.
Warehouse Receiving SOPs
Mistakes during the receiving process can lead to serious repercussions down the line—ranging from incorrect inventory counts to unsatisfied customers due to shipment errors. A robust set of ‘Warehouse Receiving SOPs’ help in maintaining accuracy in this critical aspect of warehouse operations.
The procedures may include inspection protocols upon receipt of goods; checking against invoices; rules for handling damaged items; proper documentation procedures; guidelines on efficient stowing methods; and procedures that ensure every received item is promptly registered into the inventory system.
Warehouse Fulfillment SOP
The heart of any warehouse operation lies in its ability to successfully fulfill orders accurately and quickly—a process governed by the ‘Warehouse Fulfillment SOP.’ This concentrates on systematic picking, packaging, and shipping procedures. The SOP should outline protocols for order accuracy verification; packing methods to ensure safe product transport; and efficient routing strategies on getting packages out the door in a timely manner.
By having clearly documented standard operating procedures for fulfillment, businesses can mitigate common pain points such as incorrect orders, damaged goods and delays—ultimately improving customer satisfaction.
The Importance of Area-Specific SOPs
All these SOPs for different aspects of warehouse operation play an integral part in ensuring that both workers and management have clear guidelines to follow. This not only helps in reducing errors but also significantly boosts productivity by eliminating guesswork.
Keep in mind that successful implementation of these procedures requires consistent training, monitoring, and improvements based on real-world observations and outcomes. After all, the goal is always to keep your warehouse running smoothly while constantly striving for better ways to operate.
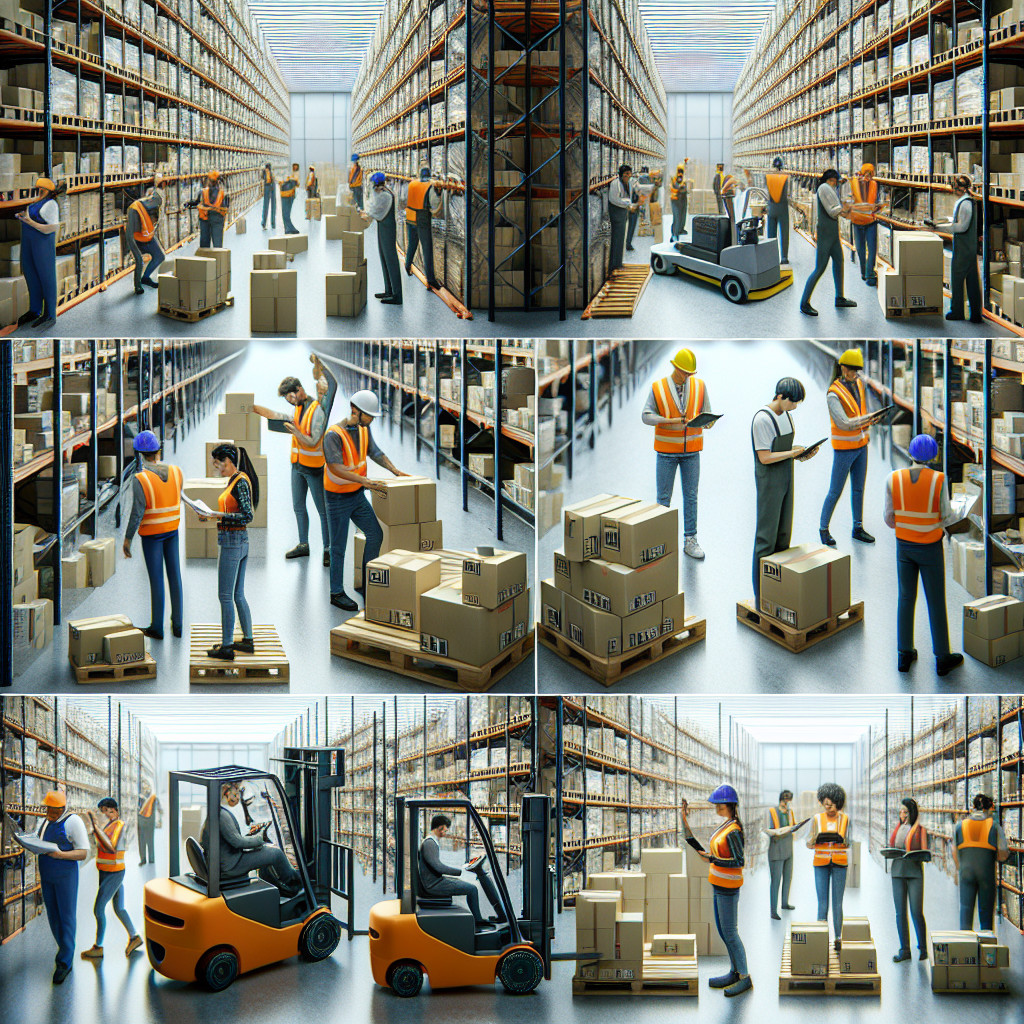
The Organizational Aspects of Warehouse SOPs
An important part of enacting strong Warehouse Standard Operating Procedures is understanding the organizational commitment required. It’s not enough to merely write up a list of procedures and hand them off to your employees. Implementing SOPs requires engagement from all levels within the organization and is a vital part of warehouse operations.
The Role of Employees
The successful execution of a ‘Warehouse Operations SOP’ heavily relies on the employees who put these plans into action daily. They are ultimately the hands that organize inventory, ensure safe working conditions, manage receiving processes, fulfill orders and carry out countless other roles. It’s crucial that they understand their respective tasks deeply and know how these fit into the broader framework of operations.
In this regard, training becomes key to familiarizing them with protocols and quality standards outlined in the SOPs. From clarifying individual responsibilities to demonstrating correct procedural actions, effective employee orientation aligns staff competence with operational expectations, thereby fostering an environment conducive for optimal warehouse functionality.
Decision-Making Authority and Responsibilities
It’s equally important that clear lines of decision-making authority within the warehouse hierarchy are established by the ‘Warehouse Management SOP’. This includes delineating who has ultimate responsibility over specific areas like inventory control or safety requirements. Regardless of size or complexity, every warehouse needs appointed leaders that can make decisions in line with set SOPs when situations arise demanding prompt resolution.
A leader’s role goes beyond just decision making. Ensuring compliance with SOPs, enabling smooth flow of communication between different sections of the warehouse, detecting deviations from standards prescribed by SOPs and taking corrective measures – all fall under their purview.
Maintaining Documentation and Enforcement
Implementing SOPs also means maintaining a meticulous record of procedures and actions taken within the warehouse. This includes everything from incoming shipments to safety incident reports. Having a well-documented trail not only offers a transparent view into operations but also provides valuable historical data that can be used for process analysis and improvement.
Enforcing SOP adherence is another key aspect. It’s essential to have mechanisms in place, such as regular audits or supervisor checks, to ensure everyone is following procedures as outlined. Non-compliance should be dealt with swiftly and firmly – this could range from additional training to disciplinary measures.
The Organizational Commitment
Awareness, understanding, acceptance and commitment are the cornerstones that make up the foundation of successful implementation of ‘Warehouse Procedures’. This involves signaling an organization-wide commitment to consistently uphold these standards.
A solid set of SOPs has direct organizational benefits including increased efficiency, reduced error rates and improved employee morale. Through clarity and structure they bring to operations, SOPs empower employees at all levels to understand their roles better and fulfill them more accurately – making your warehouse organization vibrant, organized, productive and most importantly—successful.
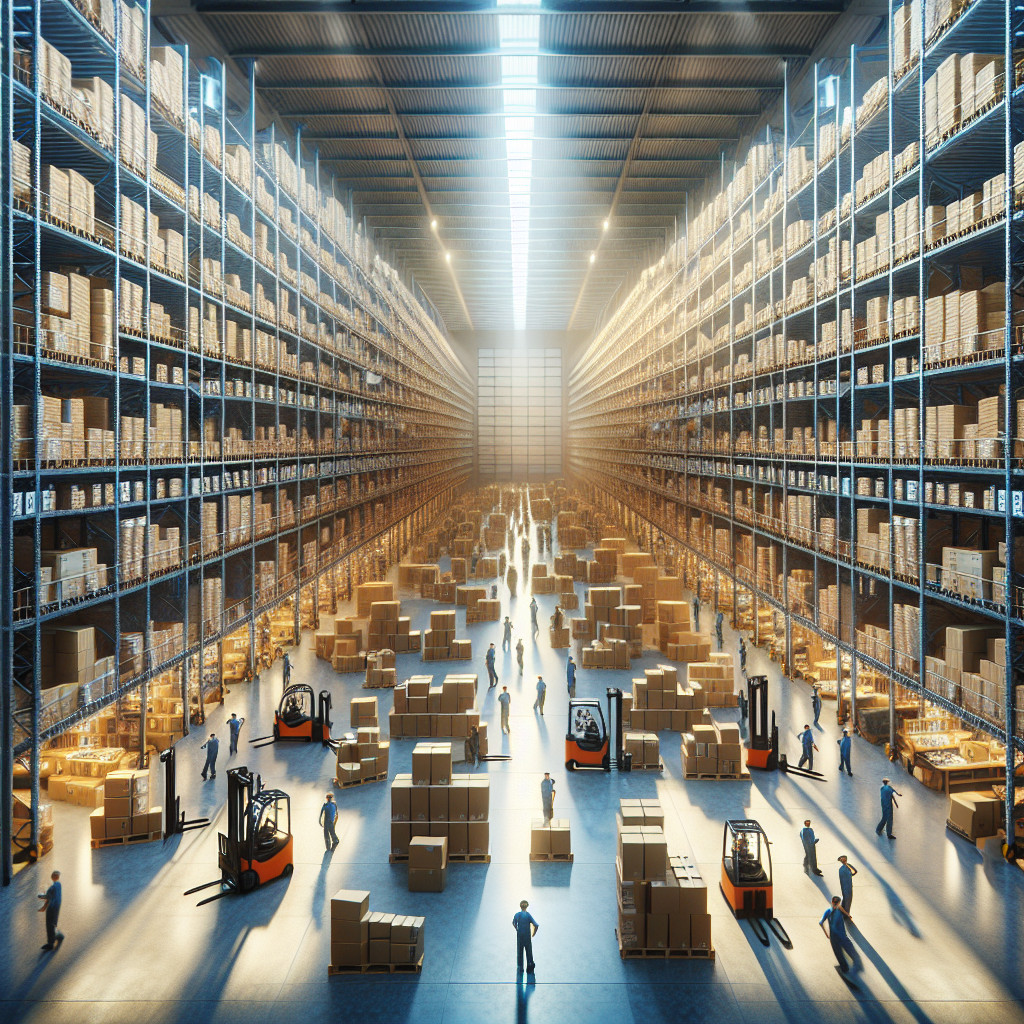
A Step-by-Step Guide on How to Script SOPs for Your Warehouse
Establishing ‘Warehouse Standard Operating Procedures’ is an essential task that requires careful planning, review and execution. Here’s a step-by-step guide on how SOPs can be scripted efficiently for your warehouse:
Identify Essential Processes in the Warehouse
The first step in crafting an effective ‘Warehouse Operations SOP’ is identifying the core processes within your warehouse operations. This includes everything from receiving goods, inventory management, order fulfillment, to safety protocols. It’s important to understand each component of warehouse operations so you can systematically break down each process into manageable steps which will form the basis of your SOP.
Create Detailed Procedure Outlines
Once you have identified all the key processes, start building a comprehensive outline for each one. As part of this step, clearly document who is responsible for what at each stage of the process and detail out expected outcomes and performance metrics. These outlines give a concrete, real-world application to your ‘Warehouse SOP’.
Draft Clear, Instructional Steps
With outlines in place, begin drafting clear, sequential steps for each procedure within the scope of your ‘Warehouse Management SOP’. These instructions should be simple and easy to comprehend by all staff members – regardless of their role or experience level. Always remember, confusing or vague instructions can result in errors and inefficiencies.
Visualize the Process Through Flowcharts
A picture speaks a thousand words—especially when it comes to conveying abstract ideas or complex procedures. Use flowcharts or other visual representations as part of your ‘Warehouse Procedures’. This helps employees better understand procedural sequences and connections between different steps.
Training and Communication
Once your SOPs are drafted, it is essential to ensure they are communicated effectively throughout the organization. Provide comprehensive training sessions that walk employees through each procedure in detail, ensuring they grasp their roles within the full context of operations.
Review and Update Regularly
Last but not least, remember that your ‘Warehouse SOP’ should never be a static document—instead, consider it as an evolving roadmap that requires regular review and updates. As your warehouse operation grows or changes, your SOPs should be revised accordingly. This ensures they remain relevant and effective at enhancing productivity and reducing potential errors.
In conclusion, these steps provide a succinct framework for scripting optimal standard operating procedures for your warehouse. It is crucial that these guidelines reflect the unique structure, processes and goals of your warehouse. With carefully drafted SOPs and consistent employee training, you can dramatically improve overall efficiency, reduce error rates and promote a safer working environment—all key elements of a successful warehouse operation.
Safety Measures and Ethics SOPs in Warehouse Management
A critical aspect often overlooked while scripting ‘Warehouse Standard Operating Procedures’ is incorporating safety measures and ethics within the wider framework of operations. Ensuring a secure, safe, and ethical environment within a warehouse is not just a legal obligation but also an essential contributor towards maintaining productivity and creating a harmonious workspace.
The Importance of Warehouse Safety SOPs
The bustling activities within a warehouse inherently pose various hazards—from manual handling injuries to accidents involving forklifts or storage systems. A well-detailed ‘Warehouse Safety SOP’ can aid in mitigating these risks by outlining safety procedures and guidelines that need to be followed diligently.
Safety SOPs should include emergency response procedures; protocols for operating heavy machinery; guidelines for wearing protective equipment like helmets, gloves, eye protection etc.; rules governing proper stacking and unstacking of goods; precautions during loading and unloading processes and procedures related to fire prevention and containment.
Implementing rigorous safety standards not only prevents accidents but also contributes towards creating an overall supportive working environment, which boosts morale and productivity—thereby cumulatively assisting in achieving operational efficiency.
Ethical Standards in Warehouse Operations
Ethics in warehouse management play an equally significant role as safety protocols. They provide a moral compass guiding interactions between employees as well as with other stakeholders such as suppliers and customers.
An optimal ‘Warehouse SOP’ integrates ethical considerations rendering them as part of daily execution of tasks. This may encompass issues like fair treatment of workers; policies against discrimination; codes governing honesty and integrity; guidelines on conflicts of interest and protocols addressing privacy concerns.
Embedding Ethics into the Warehouse Management SOP
To ensure an ethically sound environment, ethics must be embedded into the ‘Warehouse Management SOP’. This includes creating a code of conduct that outlines acceptable behavior within the warehouse. Training must also be provided to all employees—both on ethical guidelines and on their importance—in order to foster a culture of mutual respect, honesty and fair treatment.
Ethical lapses can lead to serious consequences—from deteriorating morale to legal ramifications. Hence, it is equally important to include mechanisms for reporting unethical behaviour without fear of retaliation.
Fostering Safety and Ethics Culture
Having safety procedures and ethical standards in place does not suffice unless there exists a solid commitment from management to enforce these regulations. A strategic approach involving regular audits, feedback sessions, recognizing good safety practices or ethical behaviours can aid in ingraining a safety-conscious and ethically-driven culture.
Fostering such ambiance requires constant vigilance and efforts—but its positive implications on employee welfare, operational efficiency and regulatory compliance makes it invaluable in scripting an effective ‘Warehouse Procedures’ document. Safe working conditions combined with a strong ethical climate not only aids in adhering to legal obligations but also boosts productivity and morale—once again emphasizing the significance of incorporating safety measures and ethics within your warehouse’s standard operating procedures.